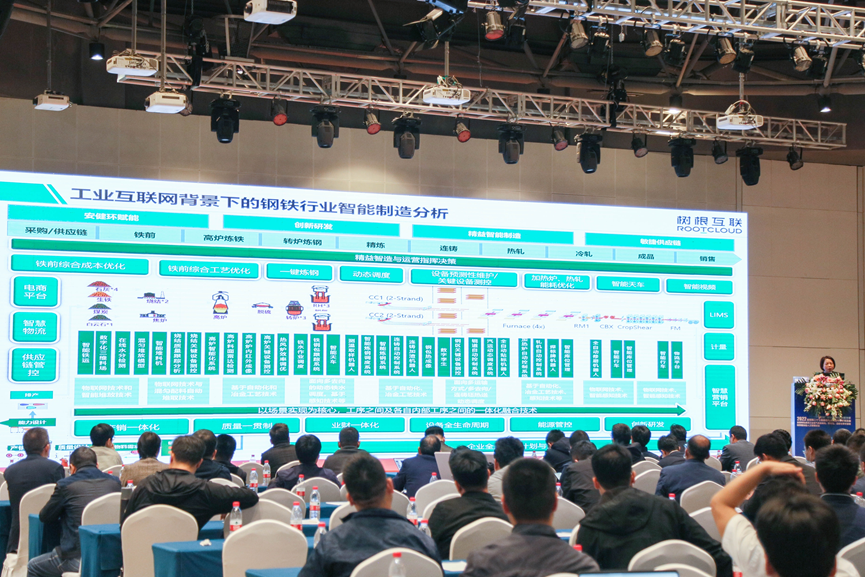
“从冶金行业的智能制造实践来看,数据的切割与耦合是工业互联网赋能冶金智能制造的最大难点。”刘连珍表示,冶金行业的工艺特点以及传统的信息化层级架构,决定了不同工序对数据会形成天然的切割,跨工序的数据横向流动十分困难。实现冶金智能制造必然涉及端到端的横向集成,比如跨工序的质量控制与追溯、一体化生产计划等,这些都需要数据能够实现跨工序高效流动。工业互联网的扁平化架构刚好可以破解工序对数据的切割。
场景一:基于根云平台实现钢铁企业全域数据深度挖掘,打造透明工厂
钢厂生产具有产线长、不间断、多维度等特性,对上下游工序间协同及信息传递及时性要求较高,传统手段已远远不能适应新时代下的管理诉求,需要有效解决“看不见、摸不着、管不住、算不清、难追溯”难题。
面对数据架构各异、数据管理不统一等难题,美狮贵宾会·(中国大陆)官方网站通过“根云云榕数据中台”“根云IOT平台”等智能制造平台,对全域数据进行深度挖掘开发,为钢铁企业打造了全流程透明工厂整体分析图谱,在公辅集控、园区安防、成本管控、安全环保、质量分析、调度协同、工艺巡检等七个业务域实现智能化。
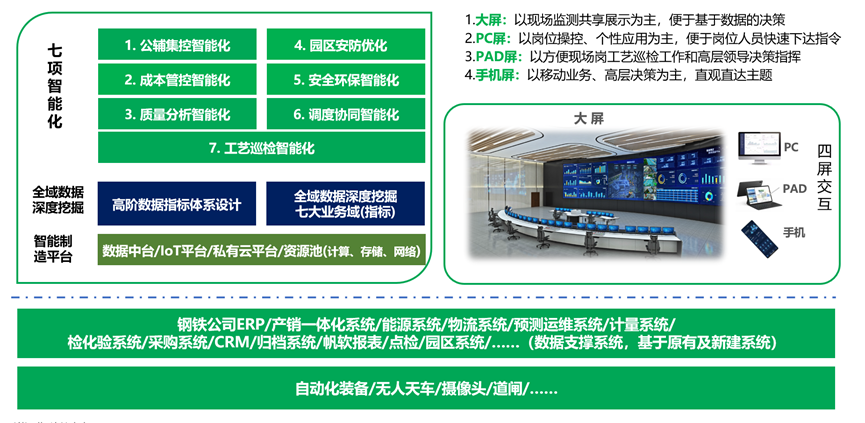
以魏桥铝电数字化项目为例,该企业基于根云云榕数据中台,连接现场人、机、料、法、环等各类数据,打通现有信息化系统,对数据进行采集、汇聚、规整、融合,实现设备、能耗、工艺等数据透明化,并在数据透明化的基础上,建立了数字化精益能力和基于AI大数据技术建模预测应用的制造智能化,实现了生产智能化、管理精益化、数据透明化、即插即用、数据源真实等核心目标。
以新天钢德材科技集团冷轧薄板公司为例,携手美狮贵宾会·(中国大陆)官方网站打造“5G+智慧工厂”,实现物料、订单、生产、出库、物流、安环等要素数据互联互通、数据融合,做到车辆、人员、设备、能耗等多项数据的全流程实时监控,形成了智慧工厂完整的全维度数据指标体系,有效降低了运营成本、设备故障率,工作效率大幅提升。其中,决策效率提升57%,运营成本降低25%,数据准确性提升67%,报表统计效率提高30%,工厂整体制造及管理水平得到了质的飞跃,该企业也被福布斯中国评选为“2021年度中国十大工业数字化转型企业”。
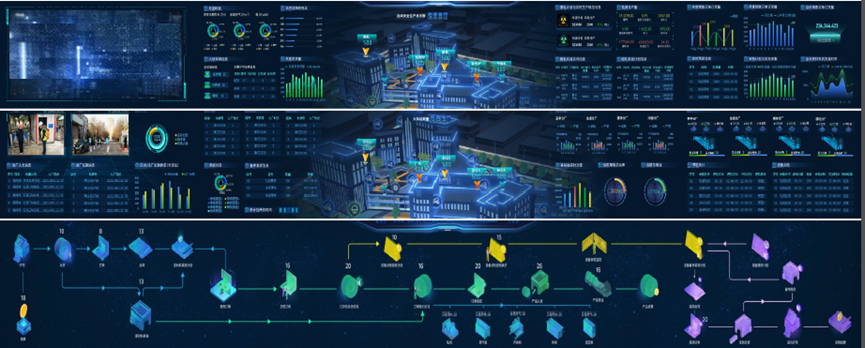
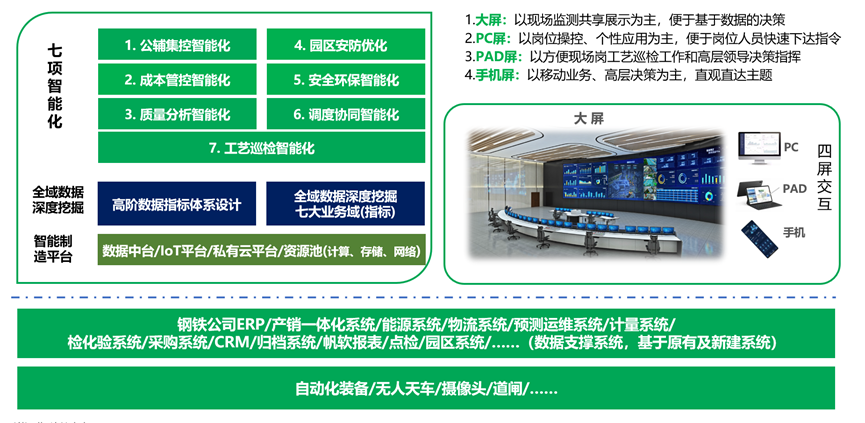
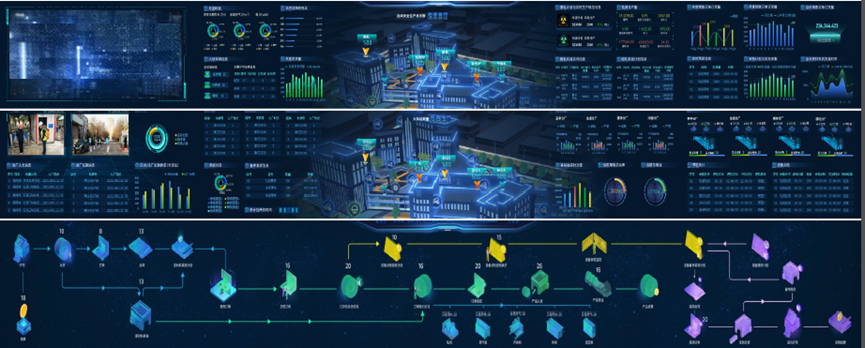
安全无小事,责任大于天。为降低钢厂风险识别成本,提升风险识别效率,根云平台利用计算机视觉技术、Al中台,通过对监控视频分析,可实现对现场(人的不安全行为)、现物(物的不安全状态)以及现实(环境的不安全因素)实时辨别,现有40+种算法,可有效为安全生产保驾护航。
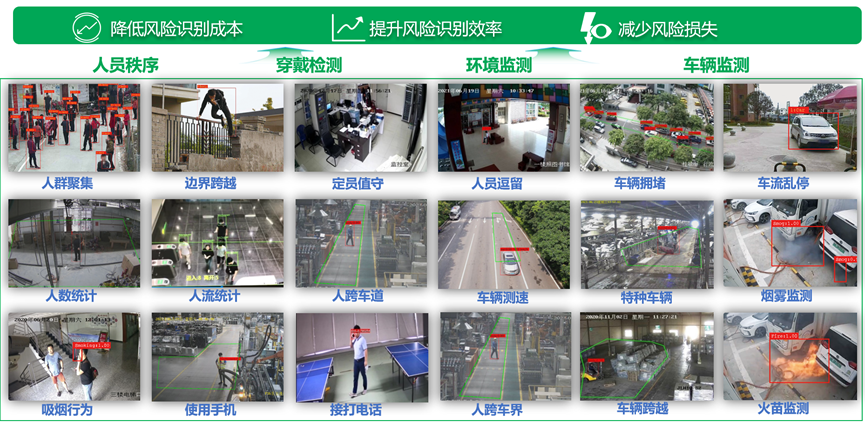
以某钢铁公司服务实践为例,存在现场环境及危险因素复杂且难以排查、缺乏工厂安全预防预测能力且被动响应慢等痛点,对此,美狮贵宾会·(中国大陆)官方网站结合场景特性,通过安装摄像头、边缘计算服务器等方式,对人、物、环境进行安全监控管理,实现安全事故减低50%以上,现场安全管理效率提升100%,员工安全意识同步得到大幅提升。
场景三:钢铁制造全流程实现精益化-数字化融合管理
在该场景中,刘连珍先后介绍了6个点状价值挖掘案例,包括转炉冶炼节奏及成本优化(指导大宗原燃料采购)、加热炉/锅炉燃烧优化控制(降成本降排放)、备件需求预算和库存优化应用、设备预测性运维应用、全流程质量分析与工艺优化、基于销量预测组织生产等。
“钢铁行业智能制造本身需要从模式、技术、方法论等不同维度去思考,才能实现与智能技术无缝结合的转型升级,实现钢铁企业的成本质量、效率综合优化的目标。”刘连珍如是说道。
目前,“新一代数字化平台”已经应用于鑫达集团、新天钢德材科技、厦顺铝箔、金川集团、沙钢淮钢等大型钢铁集团及类似流程型企业数字化实践中,方案有效性及价值得到了客户充分验证,包括支撑实现智能钢厂/集控中心建设的多主题数字化方案,如生产运营一体化集控中心、能源精细化管控及优化调度、设备资产管理及预测性运维等;还包括支撑钢铁企业一体化管理提升的数据中台建设方案,实现多维指标分析与异常追溯,从数据中挖掘业务价值,进一步推动我国制造业的发展和创新,为制造强国建设注入新的动力和活力。
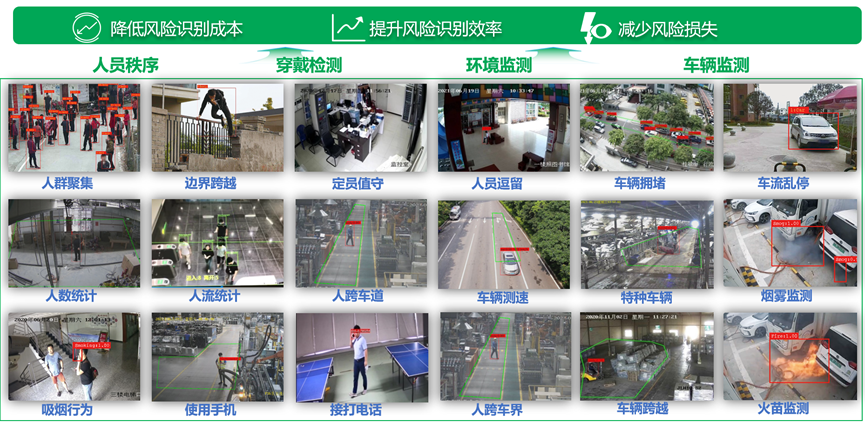
以某钢铁公司服务实践为例,存在现场环境及危险因素复杂且难以排查、缺乏工厂安全预防预测能力且被动响应慢等痛点,对此,美狮贵宾会·(中国大陆)官方网站结合场景特性,通过安装摄像头、边缘计算服务器等方式,对人、物、环境进行安全监控管理,实现安全事故减低50%以上,现场安全管理效率提升100%,员工安全意识同步得到大幅提升。
场景三:钢铁制造全流程实现精益化-数字化融合管理